When designing and purchasing precision machined products, many customers encounter common issues. Here are five of the most prevalent challenges you may face:
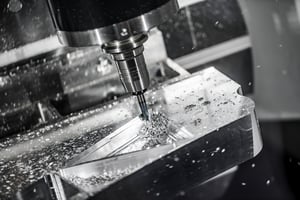
- Design Complexity and Feasibility: Creating a design that meets your specific requirements while remaining manufacturable within the capabilities of precision machining processes can be challenging. Complex designs with tight tolerances and intricate features can be more difficult to produce, leading to increased costs and/or longer lead times.
- Material Selection: Choosing the right material for a precision-machined product is crucial for its performance and cost-effectiveness. Selecting materials that offer the necessary mechanical properties, thermal characteristics, and corrosion resistance, among other considerations, can pose a significant challenge.
- Tolerances and Specifications: Defining precise tolerances and specifications is essential for precision machining. Setting precise tolerances for components can present obstacles that have the potential to impact the overall performance and fit of the end product.
- Communication and Collaboration: Effective communication between you and precision machining providers, like EEC, is critical to ensure that the design intent and specifications are clearly understood. Miscommunication can lead to misunderstandings, delays, and potential errors in the final product.
- Cost and Budget Constraints: Precision machining can be costly, especially for custom or low-volume orders. Balancing the desired specifications with budget constraints, finding the most cost-effective solutions without compromising the design or quality, can prove difficult. Additionally, it's important to factor in cost savings for large-scale production and explore strategies to optimize efficiency through manufacturability.
To address these issues, customers should:
- Engage in early and open communication with EEC to discuss design requirements and feasibility.
- Collaborate with EEC’s engineers during the design phase to optimize manufacturability.
- Consider material properties carefully and consult with material experts at EEC, if necessary.
- Clearly define tolerances and specifications based on the intended application and functional requirements.
- Request quotes and cost breakdowns to align design choices with their budget limitations.
- Request prototypes and conduct thorough testing before proceeding with larger production runs.
- Partner with EEC, an experienced and reputable company, that can offer guidance and expertise throughout the design and purchasing process.
By addressing these issues proactively, you can count on EEC to help achieve successful outcomes when designing and purchasing precision machined products that meet their performance, design, quality, and budgetary needs.